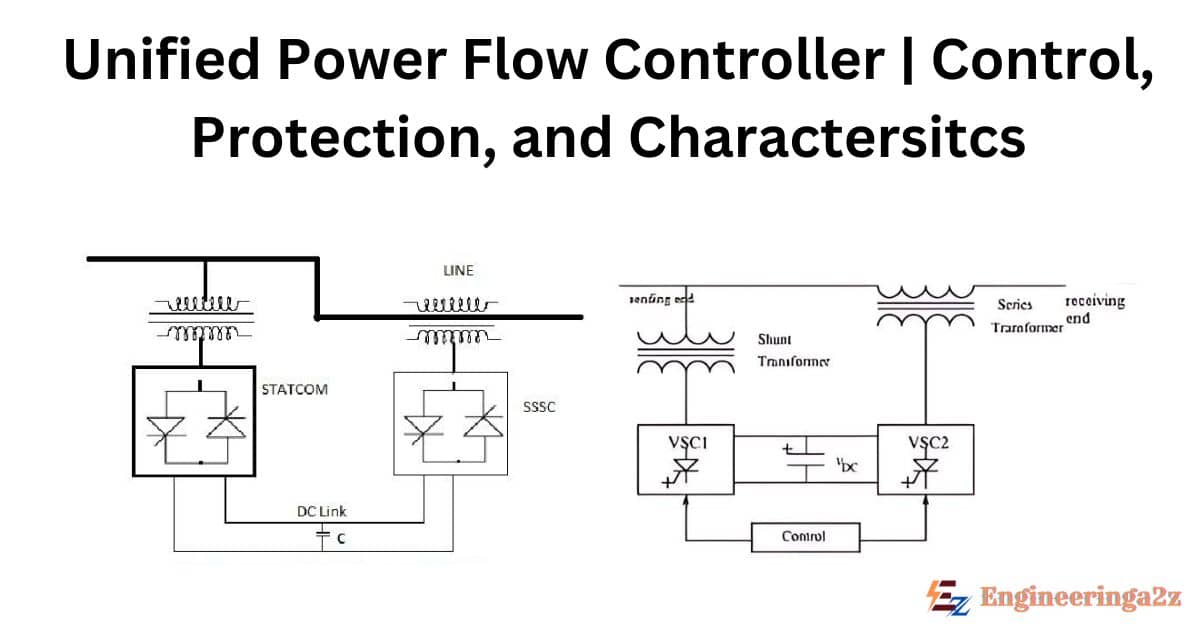
Table of Contents
UPFC
The Unified Power Flow Controller (UPFC) proposed by Gyugyi is the most versatile FACTS controller for the regulation of voltage and power flow in a transmission line. It consists of two voltage source converters (VSC) one shunt connected and the other series connected. The DC capacitors of the two converters are connected in parallel (see Fig.). If switches 1 and 2 are open, the two converters work as STATCOM and SSSC controlling the reactive current and reactive voltage injected in the shunt and series respectively the line. The closing of switches 1 and 2 enable the two converters to exchange real (active) power flow between the two converters.
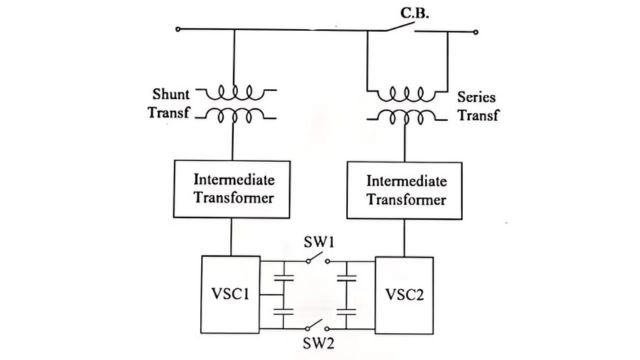
The active power can be either absorbed or supplied by the series-connected converter. As discussed in the previous chapter, the provision of a controllable power source on the DC side of the series-connected converter results in the control of both real and reactive power flow in the line (say, measured at the receiving end of the line). The shunt-connected converter not only provides the necessary power required but also the reactive current injected at the converter bus. Thus, a UPFC has 3 degrees of freedom, unlike other FACTS controllers which have only one degree of freedom (control variable).
Control of UPFC
As the UPFC consists of two converters that are coupled on the DC side, the control of each converter is taken up individually.
1. Control of the Shunt Converter
The shunt converter draws a controlled current from the system. One component of this current is Ip which is automatically determined by the requirement to balance the real power supplied to the series converter through the DC link. This power balance is enforced by regulating the DC capacitor voltage by feedback control. The other component of the shunt converter current is the reactive current, Ir which can be controlled similarly as in a STATCOM. There are two operating (control) modes for a STATCOM or the shunt converter. These are,
- VAR control mode where the reactive current reference is determined by the inductive or capacitive VAR command. The feedback signals are obtained from current transformers (CT) typically located on the bushings of the coupling (step down) transformer.
- Automatic voltage control mode where the reactive current reference is determined by the output of the feedback voltage controller which incorporates a droop characteristic (as in the case of an SVC or a STATCOM). The voltage feedback signals are obtained from potential transformers (PT) measuring the voltage V1 at the substation feeding the coupling transformer.
2. Control of the Series Converter
The series converter control is aimed at injecting a series voltage of the required magnitude and angle. These are different control modes for the series voltage listed below.
- Direct voltage injection mode where the converter simply generates a voltage phasor in response to the reference input. A special case is when the desired voltage is reactive in quadrature with the
line current. - Phase Angle Shifter Emulation mode where the injected voltage VหC is phase shifted relative to the voltage V1 by an angle specified by the reference input.
3. Operating Constraints
Six major constraints must be satisfied in scheduling the control of a UPFC in a steady state. These are:
- The upper limit on the magnitude of the shunt converter current, namely |IC| < IC max
- The upper limit on the magnitude of the voltage injected by the shunt converter.
- The upper limit on the magnitude of the voltage injected by the series converter |VC| < VC max
- Upper limit on the magnitude of the line current flowing through the series converter.
- Maximum and minimum limits on the line side voltage, VL is given by
VL min โค |VL| โค VL max - Upper limits on the magnitude of the power flow (PDC) in the DC link.
Protection of UPFC
There is an upper limit on the current flowing through the GTOs which can be turned off by applying a gate pulse. This limit is generally much higher than the nominal current rating of the converter. The latter is associated with continuous operation. When the line current increases rapidly above the critical level, under fault conditions, it is necessary to divert the current from the series converter. The bypassing of the converter may be achieved within microseconds using a thyristor bypass switch on the secondary side of the coupling transformer.
The switch must be designed to carry the maximum fault current for short periods of time. If the fault is a transient fault, the thyristor bypass switch opens when the current drops and normal operation can be resumed. If the fault is of long duration, it is necessary to initiate the closing of a mechanical bypass switch (breaker) which is located across the primary winding of the coupling transformer, in order to relieve the loading on the thyristor bypass switch. Once the primary bypass switch is closed, the re-insertion of the series transformer requires the same procedure of startup.
The series converter, during the startup has to drive a current through the primary winding of the series transformer, that matches the line current. When the match is achieved, the current in the mechanical bypass switch reduces to zero and it can be opened without creating any transients. The startup can be achieved in a few cycles after the fault clearing. Although the current through the shunt connected converter is carefully controlled under normalm operating conditions, it could exceed the critical level under fault condition.
The protective action under such conditions is to interrupt the normal gating sequence. Generally, under transient conditions, it is possible to return to normal operation within a cycle (after the interruption of the normal gating sequence). In most cases, there is no need to trip the shunt breaker. However, a major internal failure may necessitate the opening of the shunt breaker.
SSR Characteristics of UPFC
The major advantage of controllable compensation such as a combination of fixed capacitor and SSSC is to dynamically avoid resonance by the proper choice of the fixed series capacitor and meeting the required compensation using SSSC. It was also mentioned that the provision of a well-designed Subsynchronous Damping Controller (SSDC) as an auxiliary controller (with a STATCOM or SSSC) can be used to damp Subsynchronous Oscillations (SSO).
The UPFC can be viewed as a combination of STATCOM and SSSC with an additional degree of freedom (of injecting a real voltage). If this voltage is controlled to emulate positive resistance, it was observed from a case study based on the IEEE First Benchmark Model (FBM), that the critical torsional mode can be damped adequately. The shunt converter of the UPFC is connected at the electrical center of the line (considering the series injected reactive voltage). The eigenvalues for the cases (i) Vp = 0 and (ii) Vp = 0.065 are shown in Table.
It is assumed that the shunt converter regulates the bus voltage while the series converter injects a constant reactive voltage in addition to positive resistance emulation (The real power flows from the series converter to the shunt converter). It is observed from Table, that the critical torsional mode (# 3 corresponding to a radian frequency of 160) is undamped for case (i) and gets damped for case (ii). Thus a UPFC provides an inherent control for damping SSR without any SSDC. Similar results are also obtained with an IPFC.
However, IPFC connected in two parallel lines results in positive resistance in one line and a negative resistance in the other (with resistance emulation). If the net resistance in the loop is positive and can be controlled, it is possible to dampen the critical mode using IPFC.
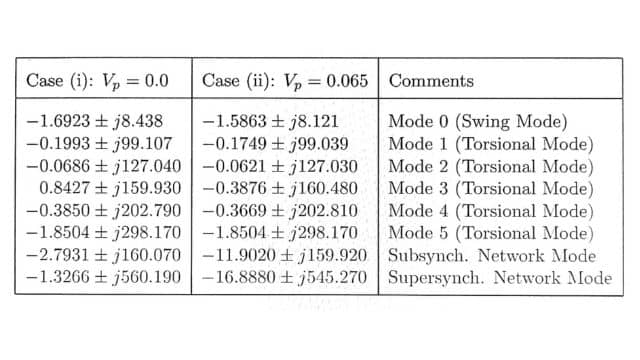
Applications of UPFC
A UPFC may be required whenever the problems of voltage and power flow are present. The planning studies are required to determine the need for a UPFC. A major advantage of a multi-converter FACTS controller is the versatility and flexibility afforded by more than one degree of freedom. With a UPFC or IPFC, 3 degrees of freedom can be utilized to regulate 3 quantities in the network – bus voltage and/or power and reactive power flow in the line(s). Such flexibility is important in the operation of restructured power systems.
Frequently Asked Questions (FAQs)
-
What does UPFC stand for?
A Unified Power Flow Controller (UPFC) helps quickly manage and balance electricity flow on high-voltage power lines, improving stability and efficiency in the power grid system.
-
What is the role of the DC link in UPFC?
A UPFC has two converters that share a capacitor and control system. These allow power to flow both ways, balancing power between the series SSSC and shunt STATCOM outputs.
Leave a Reply