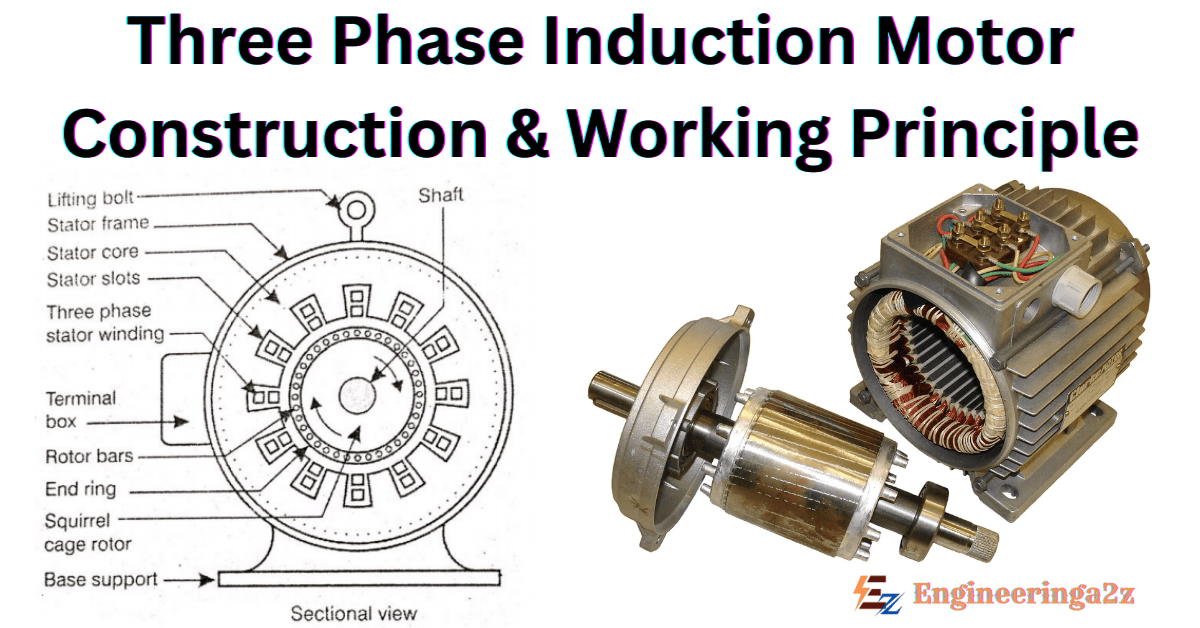
Table of Contents
Three Phase Induction Motor
The three phase induction motor is one of the A.C. motors, which is widely used for various purposes in industry. These motors never run at a synchronous speed but a little less than the synchronous speed. The speed of these motors depends upon the supply frequency.
Therefore, these motors are not generally used for speed control. However, we prefer D.C. motors where large variations of speed are required. These motors are preferred in industry because they have low price, simple & rugged construction, can be manufactured with characteristics to suit the industrial requirement.
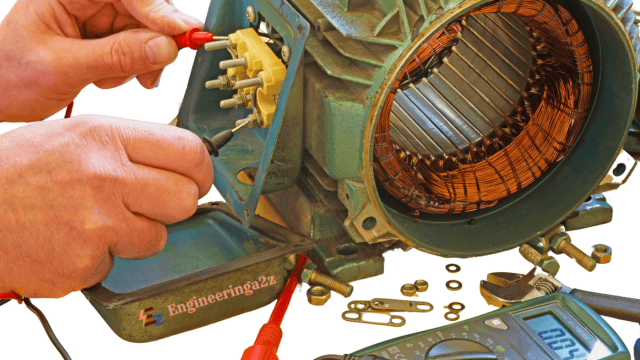
These motors differ from other types of motor, in that there is no electrical connection between the rotor & supply. The required voltage & current are induced by induction from the stator winding that is why, the name given is induction motor.
Construction of Three Phase Induction Motor
It can be better understood if we see the construction of three phase induction motor which has two major parts:
- Stationary part, known as Stator
- Rotating part, known as Rotor.
1. Stator
It is the stationary part of the motor. It has three main parts:
Frame or Yoke
It is the outer part of the three phase induction motor. Its main function of the frame is to support the stator core & stator winding. It acts as a covering, and it provides protection & mechanical strength to all the inner parts of the three phase induction motor.
Stator core
The main function of stator core is to carry the alternating flux. In order to reduce the eddy current loss, the stator core is laminated. The core is made up of thin silicon steel laminations. These are insulated from each other by varnish, the slots are cut on inner periphery of core stampings. The stator windings are placed in these slots.
Stator windings
Stator winding is made up of super enamelled copper wire. Three phase windings are placed in the stator core slots & six terminals are brought out. They may be star connected or may be delta connected. The windings are connected in star at starting.
2. Rotor
It is a rotating part of the motor. It is mounted on the shaft. It consists of hollow laminated core having slots on its outer periphery. The windings placed in these slots (rotor winding) may be one of the following two types :
- Squirrel cage rotor
- Slip ring rotor or wound rotor or phase wound rotor.
1. Squirrel cage rotor
The rotor consists of a cylindrical laminated core with parallel slots for carrying the rotor conductors. The squirrel cage rotor consists of a aluminium, brass or copper bars. These aluminium, brass or copper bars are called rotor conductors & are placed in the slots on the periphery of the rotor. The rotor conductors are permanently shorted by the copper, or aluminum rings called the end rings. To provide mechanical strength, these rotor conductors are braced to the end ring & hence form a complete closed circuit resembling like a cage & hence got its name as squirrel cage induction motor.
2. Slip ring rotor or wound rotor or phase wound rotor
The wound rotor consists a slotted armature. Insulated conductors are put in the slots & connected to form a three phase double layer distributed winding similar to the stator winding. The rotor windings are connected in star.
The open end of the start circuit are brought outside the rotor and connected to the insulated slip rings. The slip rings are mounted on the shaft with brushes testing on them. The brushes are connected to three phase variable resistors connected in star. The purpose of slip rings & brushes is to provide a means for connecting external resistors in the circuit.
Principle of Operation of 3-Phase Induction Motor
The three phase induction motor works on the principle of electromagnetic induction. When a three-phase supply is given to three-phase winding of the motor, a magnetic field is produced which rotates at synchronous speed. The rotating flux passes through the air gap and cuts the rotor conductors which are at rest. The rotor winding is short circuited, therefore, the current will flow in the rotor winding due to induced emf & a magnetic field is setup.
Now these two magnetic field interact, a torque is produced. According to Lenz’s law under the influence of this torque, the rotor starts rotating in the same direction as the rotating magnetic field.
The speed of the rotor will be always less than the speed of the field. The emf in the rotor is induced by the law of electromagnetic induction, therefore, this motor is called induction motor.
Related Posts
- Stepper Motors | Types, Parameters, and Characteristics
- Static Phase Shifting Transformer | Configurations and Improvement
- Capacitive Voltage Transformer | Working, Characteristics, and Applications
- Rotating Magnetic Field | Mathematical Analysis and Condition for Generation
- Starting and Speed Control Methods of 3-Phase Induction Motors
- Losses and Efficiency Of D.C. Machines
Leave a Reply