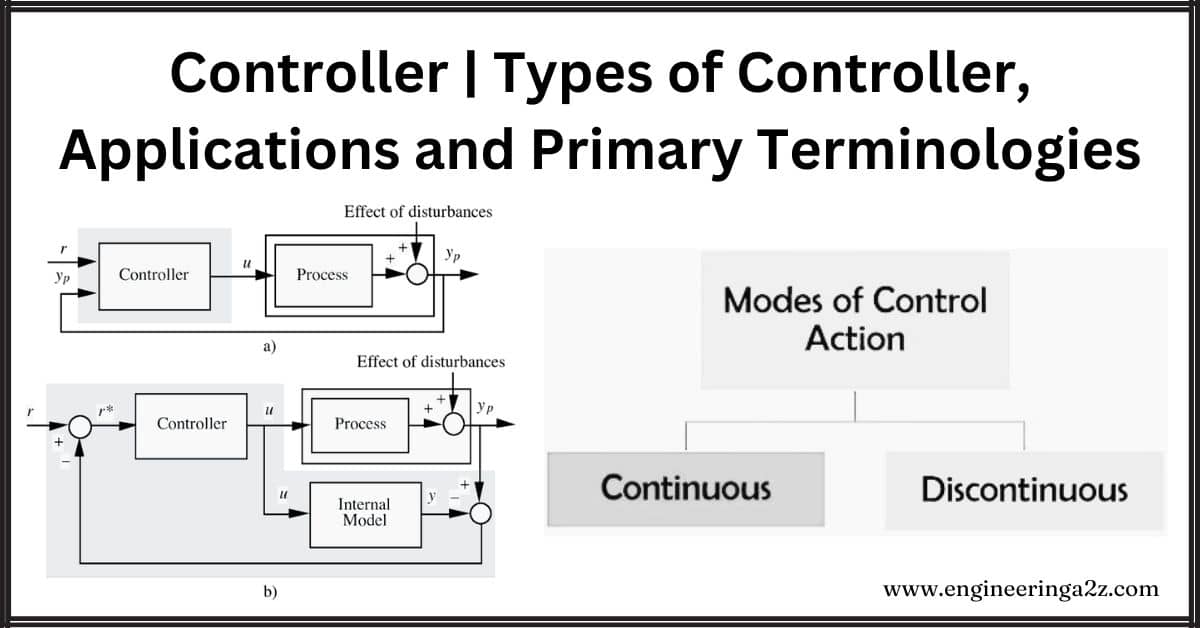
Table of Contents
What is a Controller?
Controllers are like the brains of a control system, working to keep things on track. Here’s why they’re so important:
- Getting it Just Right: Controllers make sure the system settles at the right spot, minimizing the gap between where it is and where it should be.
- Keeping Things Steady: They help make the system more stable, so it doesn’t swing wildly around the desired value.
- Clearing Up the Mess: Controllers clean up any leftover errors that might stick around in the system, making sure it’s as accurate as possible.
- Staying in Bounds: They prevent the system from overshooting its target, keeping it within acceptable limits.
- Cutting Out the Noise: Controllers filter out any unwanted signals or disturbances that could throw the system off course.
- Speeding Things Up: They can also give a boost to sluggish systems, making them respond more quickly and efficiently.
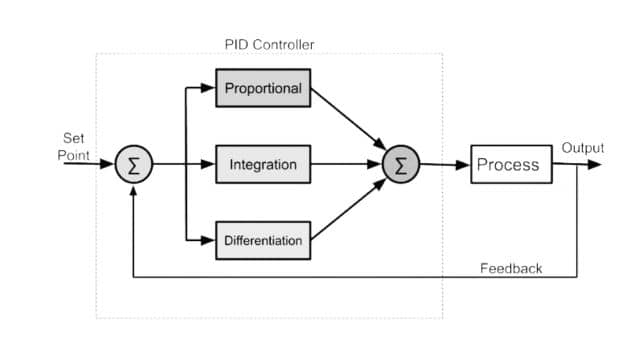
Types of Controllers
Controllers come in two main types:
- Continuous and,
- Discontinuous.
Discontinuous controllers work a bit differently. Instead of smoothly adjusting, they jump between specific values. Imagine it like a light switch – it’s either on or off, with nothing in between.
Now, depending on how many options it has, discontinuous controllers are further divided. There are two-position controllers (like a simple on/off switch), three-position controllers (which have a few more options), and multi-position controllers (which offer even more choices). It’s like having different settings on your fan – low, medium, and high. Each position represents a different level of control.
Continuous controllers use more sophisticated mechanisms compared to discontinuous ones. They can smoothly adjust the final controlling elements, like valves or motors.
In continuous controller theory, everything revolves around three main modes of operation:
- Proportional Mode: This mode adjusts the control action proportionally to the difference between the desired value and the actual value of the system. It’s like turning up the volume on your music just enough to match your preferred level.
- Integral Mode: Here, the controller looks at the accumulated error over time and adjusts accordingly. It’s like making corrections based on the overall trend, not just the current situation.
- Derivative Mode: This mode anticipates future changes by looking at how fast the error is changing. It’s like predicting traffic by how quickly the cars ahead of you are speeding up or slowing down.
These three modes work together to keep things running smoothly and on track.
- Proportional controllers.
- Integral controllers.
- Derivative controllers.
We use a mix of these modes to make sure our system behaves just right, matching the desired setting as closely as possible. Now, let’s break down these combined controllers:
- PI Controller (Proportional-Integral): This controller uses both proportional and integral modes. It adjusts the control action based on both the current error (like the difference between where you are and where you want to be) and the accumulated error over time. It’s like a chef who not only tastes the soup as it cooks but also adjusts based on how it’s been tasting throughout the whole cooking process.
- PD Controller (Proportional-Derivative): Here, we combine proportional and derivative modes. It adjusts the control action based on both the current error and how fast that error is changing. It’s like driving a car and adjusting your speed not just based on how far you are from your destination, but also on how quickly you’re approaching it.
- PID Controller (Proportional-Integral-Derivative): This is the big one, combining all three modes. It considers the current error, the accumulated error over time, and how fast the error is changing. It’s like having a chef who not only tastes the soup and adjusts based on how it’s been tasting, but also predicts how the taste will change in the future based on how the cooking process is going.
These controllers are like the brains of the operation, working together to keep things running smoothly and on target.
Applications of Controllers
Controllers are like handy tools used in different areas:
- Industrial Automation: They’re used to keep things running smoothly in factories and big machines.
- Aerospace: They help manage all sorts of things in airplanes and spacecraft, like keeping them on course and controlling autopilots.
- Automotive: Controllers are behind features like cruise control, anti-lock brakes, and managing engines in cars.
- Robotics: They’re the brains behind robots, helping them move around and navigate on their own.
- Home Automation: In smart homes, controllers make sure things like heating, cooling, and even your smart devices all work together seamlessly.
Primary Terminologies of Controllers
- Control System: It’s like a manager for a process or system, making sure everything behaves as it should.
- Controller: Think of it as the boss. It’s a device or software that tells the system what to do based on feedback or what the desired outcome should be.
- Plant: This is the system or process that’s being managed or controlled by the controller. It’s like the factory floor or the machine that’s doing the work.
- Setpoint: This is the goal or target that the system aims to reach. It’s like the bullseye on a target.
- Controlled Variable: This is the specific thing in the system that the controller is trying to keep on track. It’s like the temperature in an oven or the speed of a car.
- Feedback: Imagine someone constantly checking the work to make sure it’s going in the right direction. That’s feedback. It helps the controller know if it’s doing a good job or if adjustments are needed.
- Open-Loop Control: This is like giving instructions without checking if they’re being followed. The control action isn’t influenced by feedback.
- Closed-Loop Control: This is more like a conversation. The control system uses feedback to make sure things are on track and adjusts the control action as needed to keep the controlled variable close to the setpoint.
Frequently Asked Questions (FAQs)
-
What are the three types of controllers?
The three types of controllers are proportional controllers, integral controllers, and derivative controllers. They work together or separately to regulate systems and processes in various fields.
-
What is PID controller and its types?
A PID controller combines proportional, integral, and derivative control actions. Its types include P, PI, PD, and PID controllers, each using different combinations of these actions to regulate systems and processes effectively.
-
What are the 4 components of a controller?
The four components of a controller are:
1. Measurement Device: Monitors the system’s output.
2. Error Detector: Compares the measured output to the desired setpoint.
3. Control Algorithm: Determines the control action based on the error.
4. Output Actuator: Adjusts the system based on the control action. -
What is cascade PID control?
Cascade PID control involves using two or more PID controllers in series, where the output of one controller becomes the setpoint for another. This approach enhances control performance for complex systems.
Read Also:
- Linear Applications of Op-Amp
- Feedback Amplifier | Types, Properties, and Topologies
- Physical Sensors | Classification, Types, and Advantages
- LVDT | Construction | Principle | Advantages and Applications
- Display Devices | LCD, LED, Seven Segment, Sixteen Segment
Leave a Reply